Polyester fabrics are hugely popular and practical that continue to find new uses and new markets. After long dominating the technical textile industry, it is rapidly taking over the modern fashion, sportswear and furnishings sectors thanks to its durability, crease-resistance and outstanding quick-drying properties, as well as its cost-competitiveness against cotton.
Currently, there are two main approaches to inkjet printing on polyester.
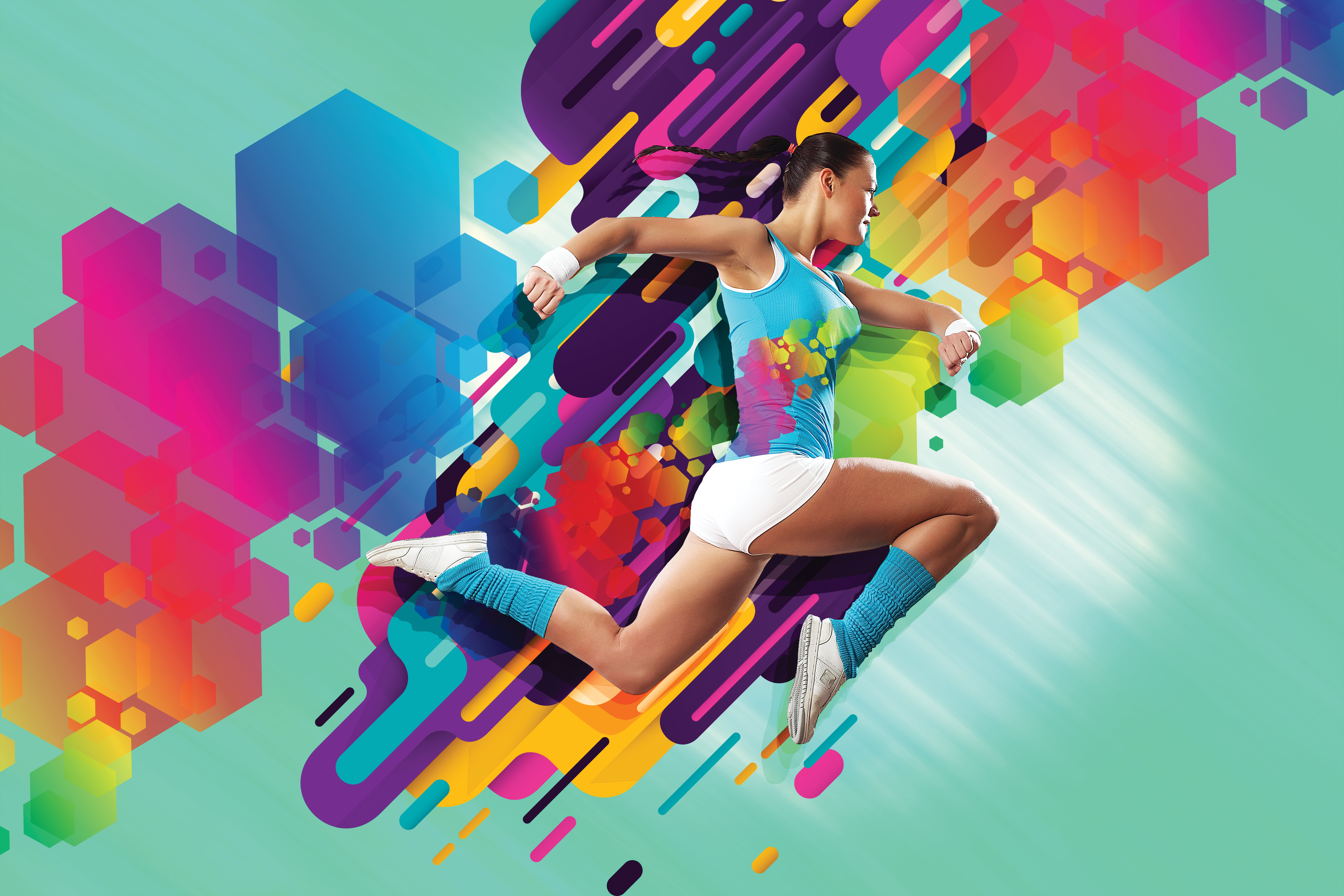
In transfer printing, sublimation inks are transferred from coated paper to fabric using a calendar to apply heat and pressure. These inks are generally based on low-energy dyes. Washing-off is optional.
In direct-to-fabric printing, disperse inks are applied to prepared fabric and fixed using a high-temperature steamer or thermo-fixing oven. These inks are usually based on mid- to high-energy dyes. Washing-off and reduction clearing are required in order to remove unfixed dye.
At first glance, sublimation inks appear to provide a faster and more straightforward process. However, direct disperse inks deliver better results and thus help printers capture market share by meeting the expectations of leading brands. Direct disperse inks excel in three key areas:
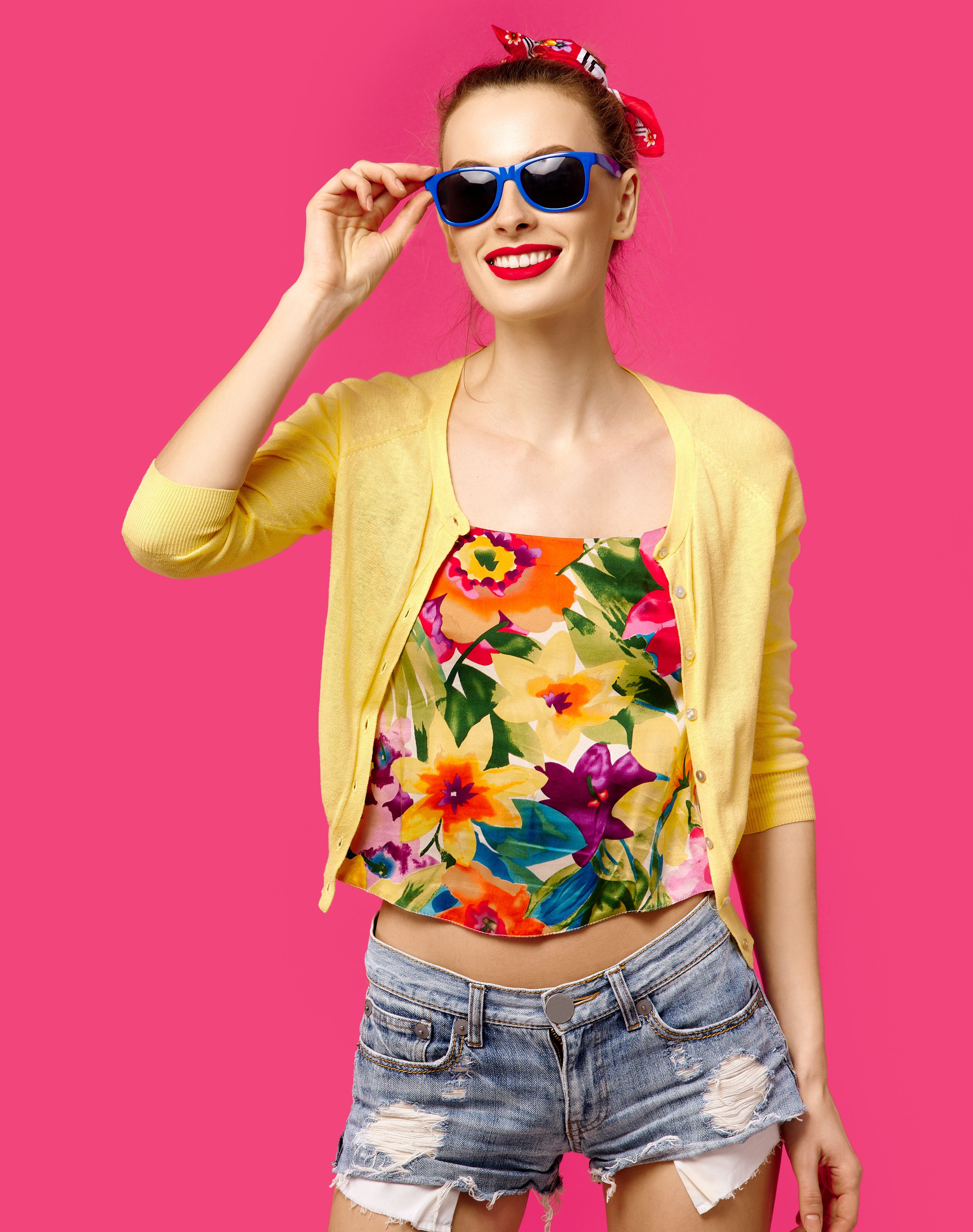
1. Wider color gamut, allowing printers to customize colors
Sublimation printing is mostly based on the CMYK color process. Printers that use direct disperse inks, on the other hand, have access to at least eight colors: orange, blue, red and grey as well as cyan, magenta, yellow and black (CMYK). This wider portfolio gives printers greater freedom to combine inks to customize colors for customers. In addition, the sublimation cyan chromophore has a bluish shade, which limits the green color space when combined with yellow; the direct disperse cyan is more turquoise, which enhances the green color space when printed with yellow.
2. Higher light-fastness properties for long-lasting good looks
Resistance to UV light is directly proportional to dye molecular size. Since sublimation inks are based on low-energy dyes made up of small dye molecules, they are much more susceptible to fading than direct disperse inks based on mid- to high-energy dyes. Light-fastness is an important factor in customer satisfaction with all types of fabrics, and especially critical in outdoor apparel and furnishings.
3. More resistant to thermal migration, protecting colors from fading
Sublimation inks are based on low-energy dyes because these allow the colorant to transform from a solid on coated paper to a gas that penetrates the fabric fibers. However, this also makes them prone to thermo-migration; if the finished product is exposed to heat, colorant can migrate around the fabric surface and cause fading. In contrast, direct disperse inks have good fastness to thermo-migration and so are more likely to keep their colors when exposed to sunlight or during home laundering or ironing.
Huntsman Textile Effects’ range of TERASIL® XKS direct disperse inks helps printers achieve outstanding results on polyester:
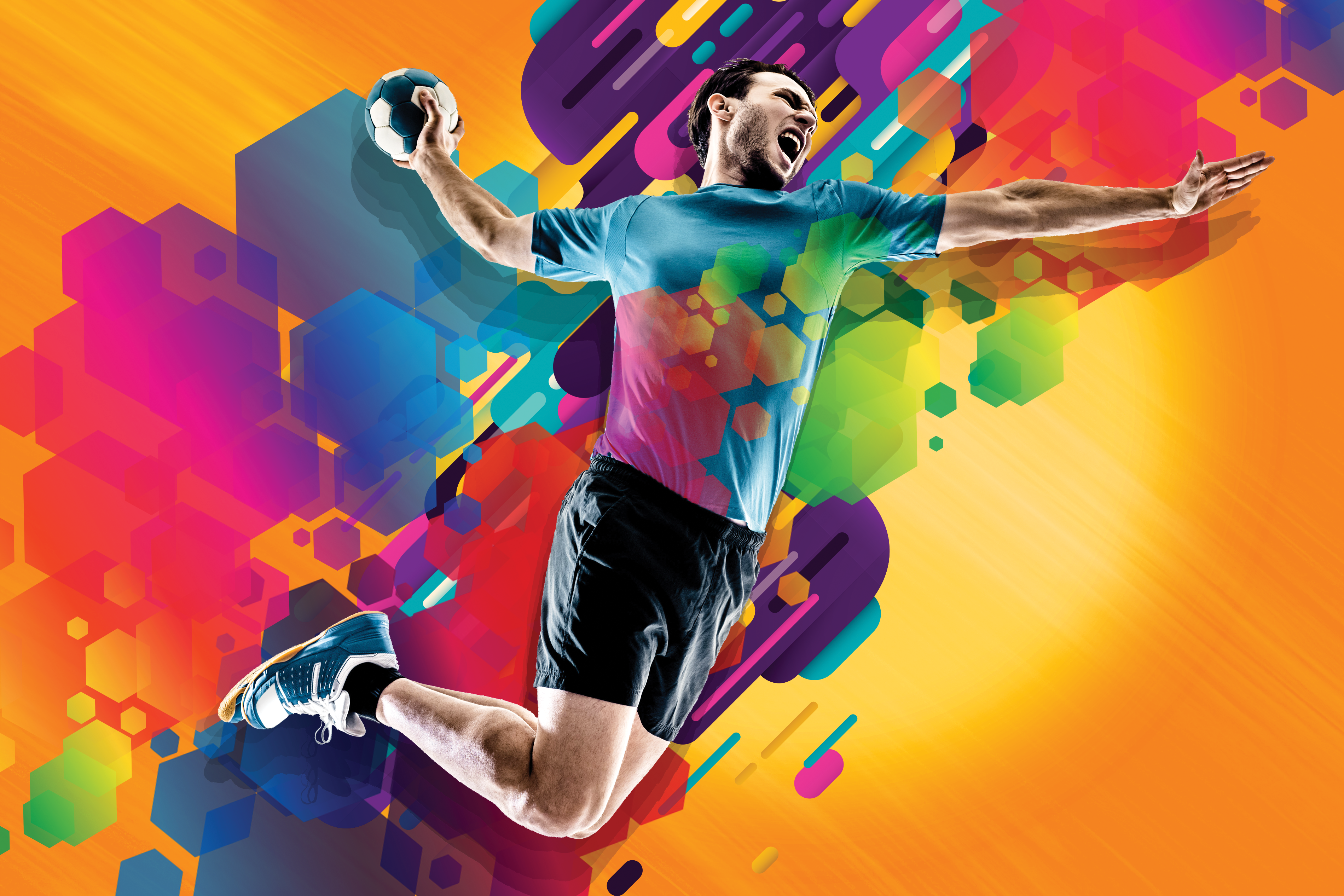
Coloristic performance: The widest gamut and deep shades comparable to analog printing
Very deep black: Maximum depth of black with reproducible results
Fastness: Excellent fastness in line with stringent requirements for apparel and home textiles
Coloristic cost control: Enhanced yield to minimize ink consumption
Productivity: Designed to maximize productivity and reliability for industrial inkjet printers with Kyocera heads
Mattia Perri, Global Technical Manager, Inkjet Application, Huntsman Textile Effects